Operating Range: The operating range selection involves a meticulous analysis of historical process data, simulation studies, and consultation with subject matter experts to delineate the precise pressure parameters the differential pressure transmitter will confront. This scrutiny encompasses identifying the typical operating pressures as well as anticipating any abnormal or transient pressure spikes that might occur due to process upsets or equipment failures. The chosen range should not only encompass the anticipated pressures but also provide a safety margin to accommodate unforeseen variations. This margin considers factors such as process variability, instrument uncertainty, and safety considerations. It necessitates a comprehensive risk assessment to evaluate the potential consequences of operating outside the designated range and implementing appropriate mitigation measures to ensure operational integrity and personnel safety.
Process Conditions: Delving into the intricacies of process conditions involves a multidisciplinary approach, encompassing fluid dynamics, thermodynamics, materials science, and chemical engineering principles. It entails a thorough examination of the fluid properties, including viscosity, density, compressibility, and corrosivity, to ascertain their influence on pressure measurements. It necessitates a comprehensive understanding of the process variables, including temperature, flow rates, and composition, and their interplay with pressure dynamics. This holistic assessment enables the selection of materials, coatings, and sealing mechanisms that can withstand the corrosive effects of aggressive fluids or extreme temperatures while maintaining measurement accuracy and reliability. It entails conducting rigorous compatibility tests and accelerated aging studies to validate the transmitter's performance under simulated process conditions and ensure its suitability for the intended application.
Accuracy Requirements: Precision in pressure measurement is paramount for ensuring process efficiency, product quality, and regulatory compliance. Defining the accuracy requirements involves a meticulous evaluation of the process criticality, tolerance limits, and regulatory standards governing the specific industry or application. It requires conducting uncertainty analyses, including error budgeting and sensitivity studies, to quantify the impact of measurement errors on process performance and product quality. Subsequently, it entails selecting a differential pressure transmitter with the appropriate accuracy class, calibration standards, and measurement uncertainty to meet the specified requirements. It necessitates implementing rigorous calibration procedures, including traceability to national or international standards, to validate the transmitter's performance and ensure its adherence to the prescribed accuracy limits throughout its operational life.
Dynamic Response: The dynamic response characteristics of the differential pressure transmitter are pivotal for capturing transient pressure fluctuations and rapid process changes in real-time. Analyzing the transmitter's dynamic response involves conducting dynamic performance tests, such as step response tests, frequency response tests, and impulse response tests, to assess its ability to track fast-changing pressure signals accurately. It necessitates leveraging advanced signal processing techniques, such as digital filtering, signal averaging, and adaptive control algorithms, to enhance the transmitter's response speed, minimize measurement lag, and mitigate the effects of noise and interference. It entails optimizing the transmitter's hardware design, including sensor technology, signal conditioning circuitry, and data acquisition systems, to improve its dynamic performance and ensure its suitability for applications requiring rapid process control and optimization.
PB8101CNF flange type
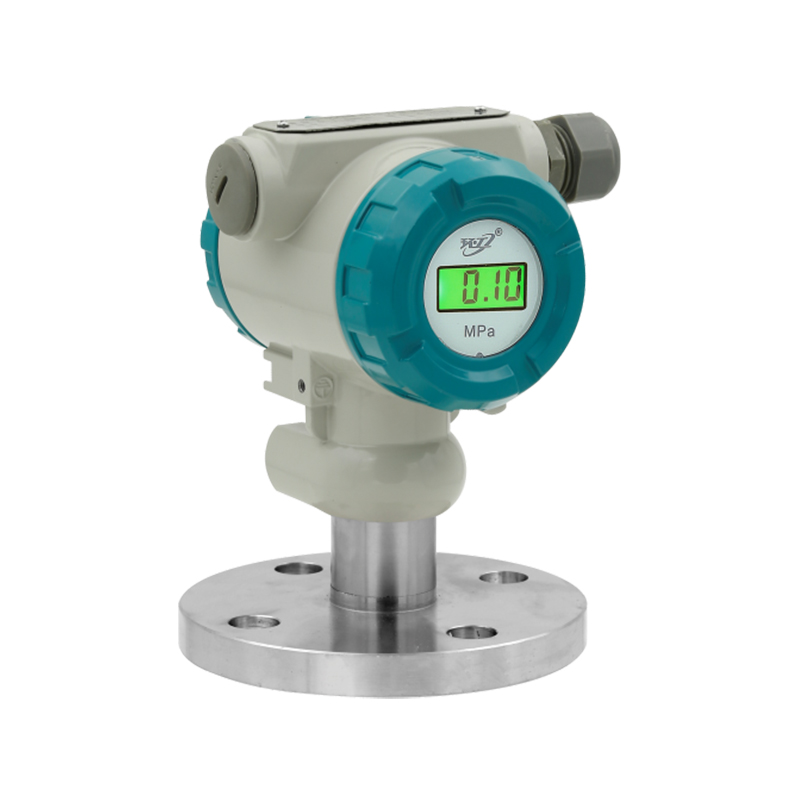