Common failure modes of pressure transmitters include:
1. Zero Drift: This occurs when the transmitter's output deviates from its true zero value. It can be caused by electronic component aging or environmental factors.
2. Span Drift: Similar to zero drift, span drift involves deviation from the correct output range. It can be caused by changes in the sensing element's mechanical properties or electronic circuitry.
3. Overpressure Damage: Exposing the pressure transmitter to pressures beyond its rated range can cause permanent damage to the sensing element or electronic components.
4. Sensor Damage: Physical damage to the sensing element due to shock, vibration, or corrosion can lead to inaccurate readings or complete failure.
5. Electrical Issues: Problems with wiring, power supply, or electronic components can cause erratic behavior or complete failure of the transmitter.
To troubleshoot these issues:
1. Calibration: Regular calibration is imperative for maintaining the accuracy and reliability of pressure transmitters. Through calibration, any deviations in zero and span values can be identified and corrected. This process involves comparing the transmitter's output against known reference standards under controlled conditions. Calibration adjustments are made using precision calibration equipment according to the manufacturer's specifications and industry standards such as ISO 9001 or NIST traceability guidelines.
2. Inspection: Routine inspection is essential to detect any physical damage or degradation in the pressure transmitter. This includes visually examining the sensing element, housing, and electrical connections for signs of wear, corrosion, or leakage. Additionally, specialized testing methods such as ultrasonic inspection or pressure testing may be employed to assess the structural integrity of the sensing element and enclosure. Any identified issues should be promptly addressed through repair or replacement of damaged components to prevent further deterioration and ensure optimal performance.
3. Overpressure Protection: Proper installation and configuration of overpressure protection mechanisms are critical to safeguarding pressure transmitters from damage caused by excessive pressure. This involves selecting and installing appropriate pressure relief devices such as relief valves, rupture discs, or pressure limiters in the system. These devices serve to divert or limit the pressure applied to the transmitter within its rated range, thereby preventing overpressure-induced failure. Additionally, periodic testing and maintenance of these protection devices are necessary to ensure their functionality and effectiveness in mitigating potential risks.
4. Electrical Testing: Thorough electrical testing is essential to diagnose and resolve any issues related to wiring, power supply, or electronic components in the pressure transmitter. This may entail conducting continuity checks, voltage measurements, and signal integrity tests using specialized testing equipment such as multimeters, oscilloscopes, or signal generators. By systematically inspecting and troubleshooting the electrical connections and components, any faults or abnormalities can be identified and rectified to restore the transmitter's functionality and reliability.
5. Environmental Considerations: Environmental factors such as temperature, humidity, and chemical exposure can significantly impact the performance and longevity of pressure transmitters. It is essential to assess the operating environment and implement appropriate measures to protect the transmitter accordingly. This may involve installing protective enclosures, selecting materials resistant to corrosion or degradation, or applying coatings or seals to mitigate the effects of harsh conditions. Additionally, proper ventilation, insulation, or heating may be necessary to maintain the desired environmental conditions within acceptable limits for optimal transmitter operation.
PB8103CNM pressure transmitters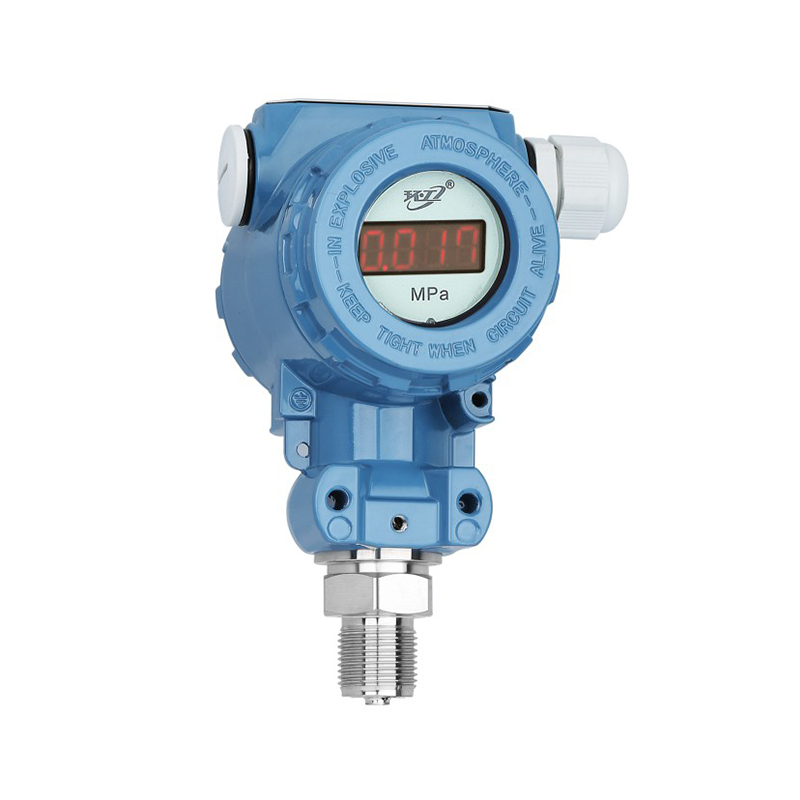