Self-heating effects in RTD (Resistance Temperature Detector) sensors can occur when the electrical current passing through the RTD element causes it to heat up, leading to a deviation from the true ambient temperature. This effect can introduce inaccuracies in temperature measurements, particularly in high-temperature applications. Here's an overview of how self-heating affects performance and measures to minimize this effect:
Impact of Self-Heating on Performance:
1.Measurement Inaccuracy: Self-heating can cause the RTD sensor to read a temperature higher than the actual ambient temperature, leading to measurement inaccuracies.
2.Response Time: The self-heating effect can also impact the response time of the RTD sensor, as the time taken to reach thermal equilibrium with the environment may be prolonged.
Measures to Minimize Self-Heating:
1.Proper Current Selection: Careful consideration must be given to the excitation current chosen for RTD sensors. Lower currents are favorable to mitigate self-heating, but the challenge lies in balancing this with the need for a robust signal.
The selection process involves a thorough assessment of the application's power consumption constraints and the desired signal strength, ensuring optimal performance under specific operating conditions.
2.Short Lead Wires: Shortening lead wires is a critical strategy aimed at reducing electrical resistance and, consequently, minimizing power dissipation within the wires themselves.
This practice is fundamental for achieving faster response times in dynamic temperature environments, significantly diminishing the adverse effects of self-heating on the overall accuracy of RTD sensors.
3.Higher Resistance Elements: The selection of RTD elements with higher resistance values inherently addresses the issue of power dissipation within the sensor.
Opting for higher resistance elements leads to reduced heat generation during current flow, effectively mitigating the self-heating effect and substantially contributing to more accurate temperature measurements.
4.Well-Designed Sensor Housings: The thermal conductivity of sensor housings plays a pivotal role in the efficient dissipation of heat generated by the RTD element.
Meticulously designed housings are essential for ensuring optimal heat dissipation, preventing the localized accumulation of heat around the RTD element. This, in turn, mitigates self-heating and preserves the high accuracy of temperature measurements.
5.External Cooling: In environments characterized by elevated temperatures, the implementation of external cooling mechanisms, including forced air or liquid cooling, becomes instrumental.
These cooling methods actively maintain the RTD sensor at a temperature lower than its surroundings, creating a controlled environment that minimizes self-heating and ensures the sensor operates within its specified temperature range.
6.Thermal Isolation: The practice of thermal isolation involves shielding the RTD element from adjacent heat sources, minimizing undesired heat transfer.
A meticulously executed thermal isolation strategy guarantees that the RTD sensor predominantly responds to the ambient temperature of interest, curtailing errors associated with self-heating and upholding the precision of temperature measurements.
7.Careful Installation: Rigorous attention to detail during the installation phase is imperative, encompassing the strategic placement of RTD sensors to avoid proximity to heat sources and meticulous consideration of ventilation requirements.
A well-executed installation minimizes external factors that could contribute to self-heating, establishing a robust foundation for the accuracy of temperature measurements across diverse operational scenarios.
Thread mount lead type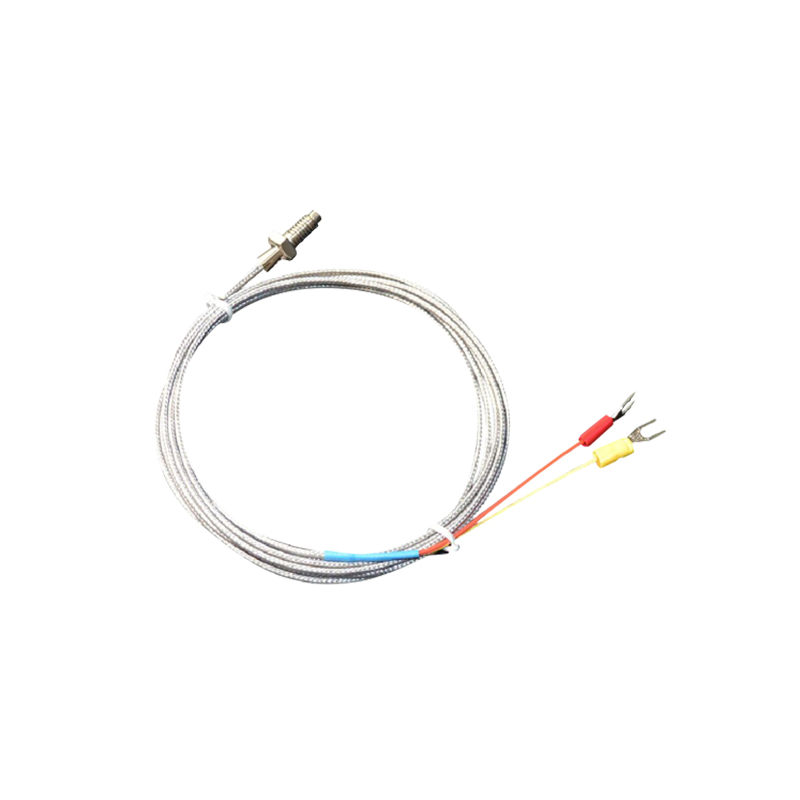