Handling foam and turbulence in liquids is a common challenge for level sensors, as these factors can introduce measurement errors. Several technologies and strategies are employed to minimize these errors:
Frequency Modulated Continuous Wave (FMCW) Radar: FMCW radar level sensors excel in liquid level measurement by employing a continuous wave with modulated frequency. This modulation allows the sensor to discriminate between the liquid surface and potential interference from foam or turbulence. The sophisticated analysis of frequency-modulated signals enhances the accuracy and reliability of measurements in challenging environments with varying substances.
Guided Wave Radar (GWR): GWR sensors feature a probe that extends into the liquid, guiding a microwave or electromagnetic wave. This design minimizes the impact of foam or turbulence on signal integrity, enabling precise level measurements. GWR technology is particularly effective in overcoming challenges posed by varying dielectric constants, making it suitable for applications where accuracy is paramount despite changing liquid compositions.
Capacitance Level Sensors: Capacitance sensors leverage changes in the electrical properties of the material between the sensor and vessel wall. This inherent capability makes them less susceptible to errors induced by foam, as the measurement is primarily influenced by the dielectric constant of the liquid. The resilience to interference enhances the sensors' accuracy and reliability in scenarios where foam or turbulence is a common occurrence.
Ultrasonic Level Sensors with Advanced Signal Processing: Ultrasonic sensors utilize sound waves for level measurements, and those with advanced signal processing capabilities excel in distinguishing genuine level changes from disturbances. By implementing sophisticated algorithms, these sensors can filter out undesired echoes and reflections caused by foam or turbulence. This ensures a more precise representation of the actual liquid level, contributing to consistent and reliable measurements.
Vibration Level Sensors: Vibrating fork or rod level sensors utilize changes in vibration frequency to detect the presence of liquid. When faced with foam, these sensors dynamically adjust their response, maintaining accuracy in level measurements. The adaptive nature of vibrating sensors makes them well-suited for applications where foam or turbulence is a recurring challenge, ensuring dependable performance in diverse operational conditions.
Multi-Variable Level Sensors: Sensors incorporating multiple variables, such as temperature or pressure, offer a holistic approach to level measurement. This comprehensive analysis allows these sensors to compensate for variations introduced by foam or turbulence, providing a nuanced and accurate representation of the liquid level. The consideration of additional parameters enhances the sensor's ability to adapt to dynamic process conditions.
Signal Averaging and Filtering: Many level sensors employ advanced signal processing techniques, including signal averaging and filtering. These methods enhance data quality by smoothing variations caused by foam or turbulence. By averaging multiple readings and applying filters to eliminate noise, these sensors deliver stable and reliable measurements, especially in applications where occasional disturbances are prevalent.
Advanced Signal Processing Algorithms: Level sensors equipped with advanced signal processing algorithms exhibit a heightened ability to analyze intricate signal patterns. By intelligently discerning genuine level changes from disturbances like foam or turbulence, these algorithms contribute significantly to the sensor's capability to deliver accurate and consistent measurements in dynamically changing liquid environments.
Magnetoresistive strip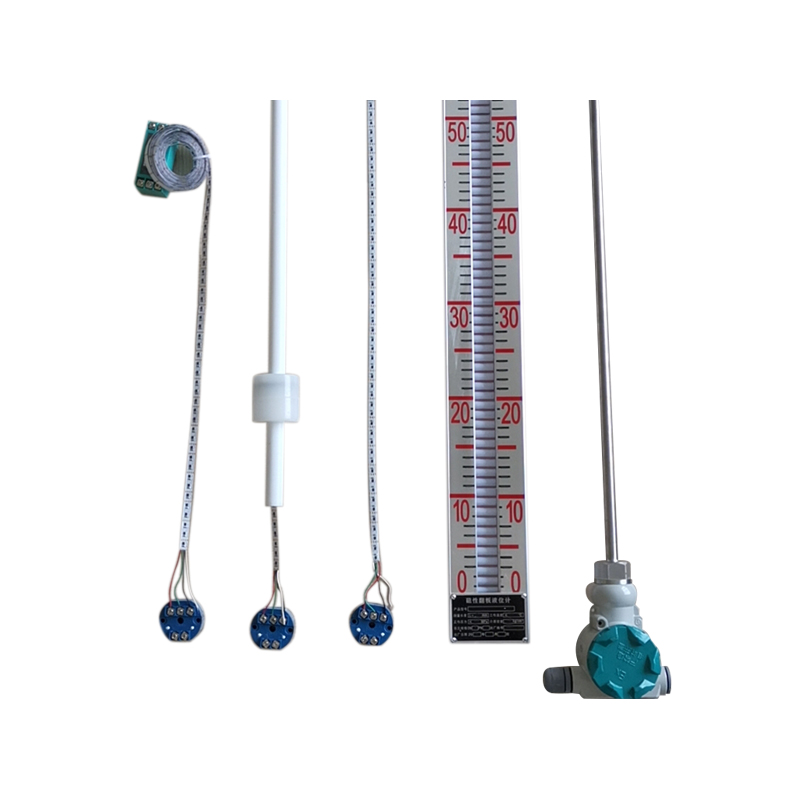