The most common tension sensor is the resistance strain gauge, which is a robust, durable and reliable sensor product. In order to ensure its accuracy, there are still some problems that need to be paid attention to in the process of installation and use. Here is a brief introduction to you:
1. The
pressure sensor should be handled with care, especially for the small-capacity sensor using alloy aluminum material as the elastic body, any shock or drop caused by vibration is likely to cause a large output error.
2. When designing the loading device and installing it, it should be ensured that the action line of the loading force coincides with the force axis of the tension sensor, so as to minimize the influence of inclined load and eccentric load.
3. In terms of level adjustment. If a single tension sensor is used, the installation plane of its base should be adjusted with a spirit level until it is level; if multiple sensors are measured at the same time, the installation surface of their base should be kept on a horizontal plane as much as possible. The purpose of this is The main reason is to ensure that the force that each sensor is subjected to is basically the same.
4. Select the rated load of the sensor used according to the range of the tension sensor in this description.
5. The base mounting surface of the sensor should be as smooth and clean as possible, without any oil stains or adhesive films. The mounting base itself should have sufficient strength and rigidity, usually higher than that of the sensor itself.
6. The sensor shell, protective cover, and bow | wire connectors are all sealed and are not allowed to be opened by households.
7. In order to prevent chemical corrosion, the outer surface of the tension sensor should be smeared with terroir forest. It should be avoided from direct sunlight and the use of the stage where the ambient temperature changes drastically. 8. When unavoidable, protective or mitigation devices should be installed.
9. In order to prevent the large current from directly passing through the sensor body and damaging the sensor, it is forbidden to carry out electric welding after the sensor is installed.
10. Add a bypass device made of copper braided wire at both ends of the tension sensor loading device.
11. The cable should not be lengthened by itself. When it is really necessary to lengthen, it should be soldered at the joint and added with moisture-proof sealant.
12. It is best to use some baffles to cover the sensor around the tension sensor. The purpose of this is to prevent debris from falling into the moving parts of the sensor and affecting its measurement accuracy.
13. The cable of the sensor should be kept away from strong power supply lines or places with pulse waves. When the competition cannot be avoided, the cable of the tension sensor should be inserted into the iron pipe separately, and the connection distance should be shortened as much as possible.
14. Determine the rated load of the sensor used according to the range of the tension sensor in this description. Although the tension sensor itself has a certain overload capacity, it should be avoided as much as possible during installation and use. Sometimes a short-term overload may also cause permanent damage to the sensor.
15. In the case of high precision use, the tension sensor and instrument should be used after preheating for 30 minutes.
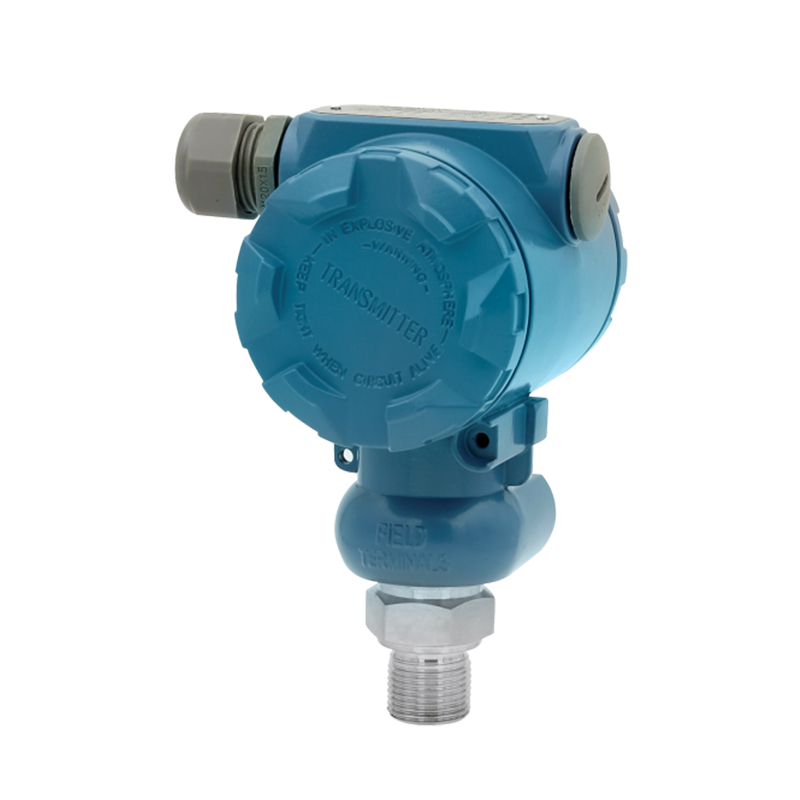
PB8100CNM pressure transmitters
Ningbo Qingyang Automation Technology Co., Ltd. is famous China Industrial Pressure Transmitters Manufacturers and OEM/ODM pressure sensors Factory. We have advanced and complete top-notch testing equipment in the industry, physical testing laboratories, automatic pressure calibration equipment, automatic temperature calibration equipment, customized differential pressure transmitters etc. The above equipment can fully ensure the provision of high-precision final wholesale differential pressure transmitters to customers, and can ensure that customers can meet all-round testing requirements for physical and chemical properties of materials, high-precision geometric dimension testing, etc.