Ensuring that a level transmitter can handle harsh environmental conditions like high temperatures or corrosive substances is crucial for many industrial applications. Here are some points to consider:
Temperature Range: Understanding the temperature range capability of the level transmitter involves examining not only its operational limits but also its performance characteristics across the entire spectrum. For instance, transmitters designed for high-temperature applications may incorporate specialized materials like Inconel or ceramic components to withstand thermal expansion and maintain measurement accuracy. Conversely, in low-temperature environments, considerations such as insulation effectiveness and material resilience against brittleness become paramount. The transmitter's ability to withstand rapid temperature fluctuations without compromising its structural integrity or calibration stability is a critical aspect to evaluate.
Corrosion Resistance: Assessing the corrosion resistance of a level transmitter involves a detailed analysis of its construction materials and protective measures. Stainless steel, known for its corrosion-resistant properties, is a common choice for wetted parts in many transmitters. However, in highly corrosive environments, exotic alloys such as Hastelloy or titanium may be necessary to ensure long-term reliability. Surface treatments like electro-polishing or specialized coatings such as PTFE (Polytetrafluoroethylene) can enhance the transmitter's resistance to aggressive chemicals or acidic solutions. Understanding the specific corrosion mechanisms at play, such as pitting or stress corrosion cracking, allows for targeted mitigation strategies to be implemented, thus prolonging the transmitter's service life and reducing maintenance costs.
Enclosure Ratings: The enclosure rating of a level transmitter provides crucial insight into its ability to withstand environmental ingress and maintain operational integrity. A comprehensive understanding of the IP (Ingress Protection) or NEMA (National Electrical Manufacturers Association) ratings ensures compatibility with the application's environmental conditions. Factors such as the presence of dust, moisture, water jets, or immersion depth dictate the appropriate enclosure rating required. Moreover, considerations extend beyond static conditions to encompass dynamic scenarios such as vibration resistance, impact resistance, and UV (Ultraviolet) stability, particularly in outdoor installations. Adhering to stringent enclosure standards not only safeguards the transmitter against physical damage but also ensures compliance with regulatory requirements and industry best practices.
Chemical Compatibility: Evaluating the chemical compatibility of a level transmitter involves a comprehensive review of the materials exposed to the measured substance and their susceptibility to degradation or chemical attack. Detailed chemical compatibility charts, material data sheets, and compatibility testing protocols aid in identifying potential interactions between the transmitter's components and the process fluid. Factors such as temperature, concentration, pH, and presence of impurities influence the degree of material compatibility required. In instances where standard materials lack sufficient resistance, custom-engineered solutions such as fluoropolymer coatings, ceramic coatings, or exotic material options may be explored. Furthermore, proactive measures such as regular material inspections, corrosion monitoring, and fluid analysis protocols mitigate the risk of unexpected failures and ensure uninterrupted operation in challenging chemical environments.
Sealing Mechanisms: The effectiveness of sealing mechanisms employed in a level transmitter directly influences its ability to maintain environmental integrity and prevent moisture ingress or fluid leakage. A multi-tiered approach to sealing, encompassing primary seals, secondary seals, and redundant barriers, enhances reliability and mitigates the risk of seal failure. Various sealing technologies such as O-rings, gaskets, compression fittings, and hermetic seals offer distinct advantages depending on the application requirements and environmental conditions. Furthermore, factors such as material compatibility, compression force, surface finish, and seal geometry play pivotal roles in optimizing sealing performance and longevity. Regular inspection, testing, and maintenance of seals ensure continued effectiveness and minimize the likelihood of costly downtime or safety hazards arising from seal breaches.
PB8601 submersible level transmitter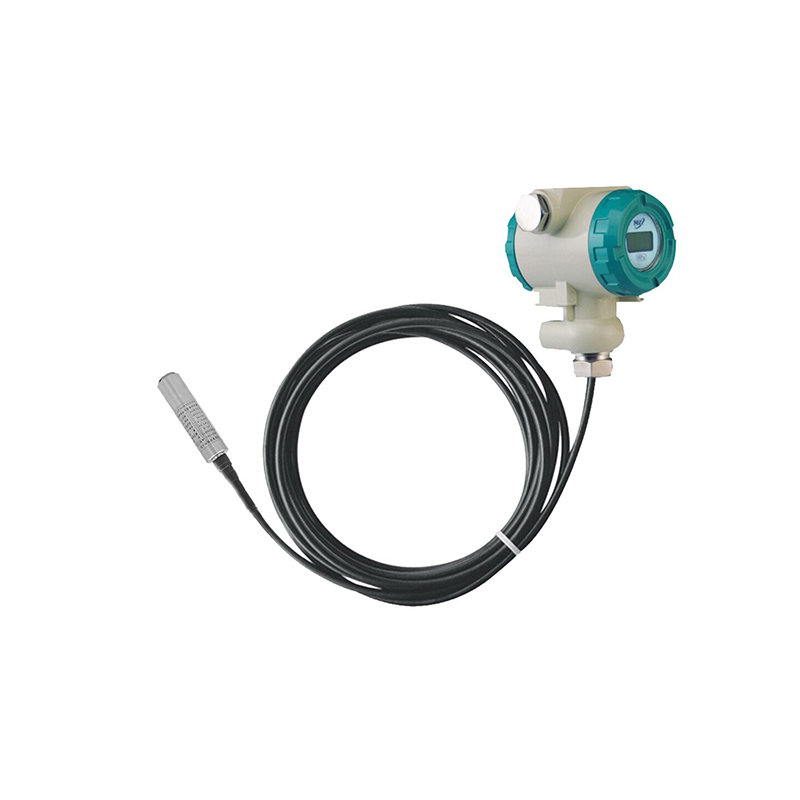